The researchers at Beijing Shougang have worked tirelessly to develop a new aluminum alloy, which has many desirable properties. This alloy features high strength, excellent thermal stability, and heat resistance, which ensures that parts built with this material are robust and can withstand high loads with relative ease.
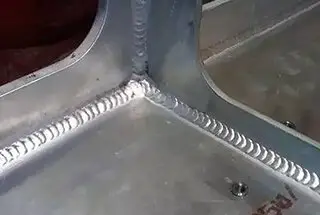
This high-temperature aluminum alloy is ideal for AM because it can be melted and re-solidified repeatedly without deformation or loss of strength, making it an ideal candidate for 3D-printing. The Beijing Shougang team has worked with a partner - though the brand name has not been revealed - to create aerospace components using this material for commercial production.
To achieve this feat, the researchers had to overcome many difficulties. In conventional manufacturing, aluminum is not used for high-temperature components because it is susceptible to deformation and loss of strength at high temperatures. Despite these challenges, the Beijing Shougang team has been able to find a way to produce the material in a way that allows it to retain its strength and durability even at temperatures up to 300 degrees Celsius.
The ability to produce lightweight, high-strength, high-temperature materials through AM is exciting for the aerospace industry. It opens up the possibility of creating parts such as engine components, exhaust nozzles, and heat shields that can withstand extreme temperatures associated with space travel and protect the spacecraft and crew from the heat generated during re-entry.
This new collaboration between Beijing Shougang and their partner is significant as it demonstrates how two companies can leverage their unique specialties to develop new materials and components that solve real-world problems. Beijing Shougang is a specialized manufacturer of special alloy wires and strips of resistance heating alloys, electrical resistance alloys, stainless steels, and spiral wires for industrial and domestic applications.
In contrast, their partner's expertise lies in AM, which is the manufacturing of intricate components layer-by-layer using a digital file. They specialize in bringing a design to life, and this expertise is essential when it comes to creating complex aerospace components that require precision and accuracy.
According to the CEO of Beijing Shougang, the high-temperature aluminum alloy developed by the company has been extremely well received by their partner, who has acknowledged that the material has exceeded their expectations in various trials and tests.
The high-temperature aluminum alloy developed by Beijing Shougang offers exciting possibilities for the aerospace industry. It has the potential to revolutionize the way we make parts and components, making it possible to achieve greater efficiency, durability, and strength. While the technology is still in the early stages, it is clear that the potential benefits are enormous, and as further research is conducted, the opportunities for the industry will continue to expand.
In conclusion, Beijing Shougang Gitane New Materials Co., Ltd. announcement of the development of a high-temperature aluminum alloy that allows for component manufacturing using AM technology is a significant step forward for the aerospace industry. The ability to produce high-strength, lightweight components that can withstand extreme temperatures and loads will enable the industry to create more advanced and efficient designs that were previously not possible. The new technology represents the continuation of the trend towards the mass adoption of bolder additive manufacturing techniques in the aerospace industry, signaling a great period of innovation and development ahead in the field.